WASTE WATER TREATMENT FOR ELECTROPLATING AND POWDER COATING

OUR PIONEERING WASTE WATER TREATMENT FOR WET-CHEMICAL PRE-TREATMENT
THE CRITICAL POINT IN ELECTROPLATING AND POWDER COATING - WASTEWATER TREATMENT
Electroplating plants and powder coating include the following types of surface treatment for metal (steel, aluminium, magnesium, etc.) and plastics:
- Cleaning (e.g. degreasing)
- Pickling and decapping (creating surface roughness, e.g. aluminium)
- Protecting and activating (conversion coating, passivation)
A high quality of water is required for all steps in the electroplating process. Wastewater treatment of the rinsing water is also becoming increasingly important, as the quality of the rinsing water plays a decisive role in the adhesion of the powder.
OUR EVAPORATION TECHNOLOGY AS A SUSTAINABLE SOLUTION FOR ELECTROPLATING WASTE WATER TREATMENT
In order to keep the rinsing water quality consistently high, we rely on future-oriented atmospheric evaporation technology. It offers many advantages in terms of energy (up to 50 % energy savings compared to a conventional vacuum evaporator). The distillate quality also leaves nothing to be desired, which is why we are able to keep the water usable in a circulation system. In addition, our use and quantity of chemical agents in electroplating waste water treatment is exemplary, especially in terms of effectiveness and ecological compatibility.
THE STRENGTHS OF OUR SUSTAINABLE EVAPORATOR SYSTEM ARE PARTICULARLY EVIDENT IN THESE AREAS:
- Degreasing baths
- Rinsing water after degreasing
- Pickling waste water (here, too, we impress with viable solutions)
- Rinsing water after pickling
- Rinsing water from iron phosphating
- Rinsing water from zinc phosphating
- Rinsing water from chromium-free conversion/passivation
- Rinsing water from nanoceramics
Proper preparation of your waste water also makes a significant contribution to the quality of the distillate. This is why our system has a modular design consisting of individual components (e.g. bag filter unit, pH adjustment and IBC filling station, e.g. for the concentrate), which prepare the waste water for the evaporator. This also ensures significant energy savings and greatly reduced disposal costs for the concentrate.
THERE IS NO STANDARD SOLUTION - WE ALWAYS TAKE CARE OF YOU INDIVIDUALLY!
Low energy costs and low disposal costs combined with the highest distillate quality are our priority. Fully automatic waste water treatment in the electroplating process is therefore a matter of course for us. This also includes the use of cleaning solutions for the waste water system. High waste water availability is always our top priority.
So that we can provide you with targeted advice, we always start by analysing your specific task, your current situation. We then carry out a professional implementation. We take care of everything, right down to the last detail.
THIS MEANS: COMMISSIONING, TRAINING AND AFTERSALES, ALL FROM A SINGLE SOURCE - SO THAT YOU NOT ONLY GET STABLE WATER VALUES, BUT ALSO A SMOOTH OPERATING PROCESS!
USER EXAMPLE
The ET evaporator in use at Geberit Mapress
Product groups
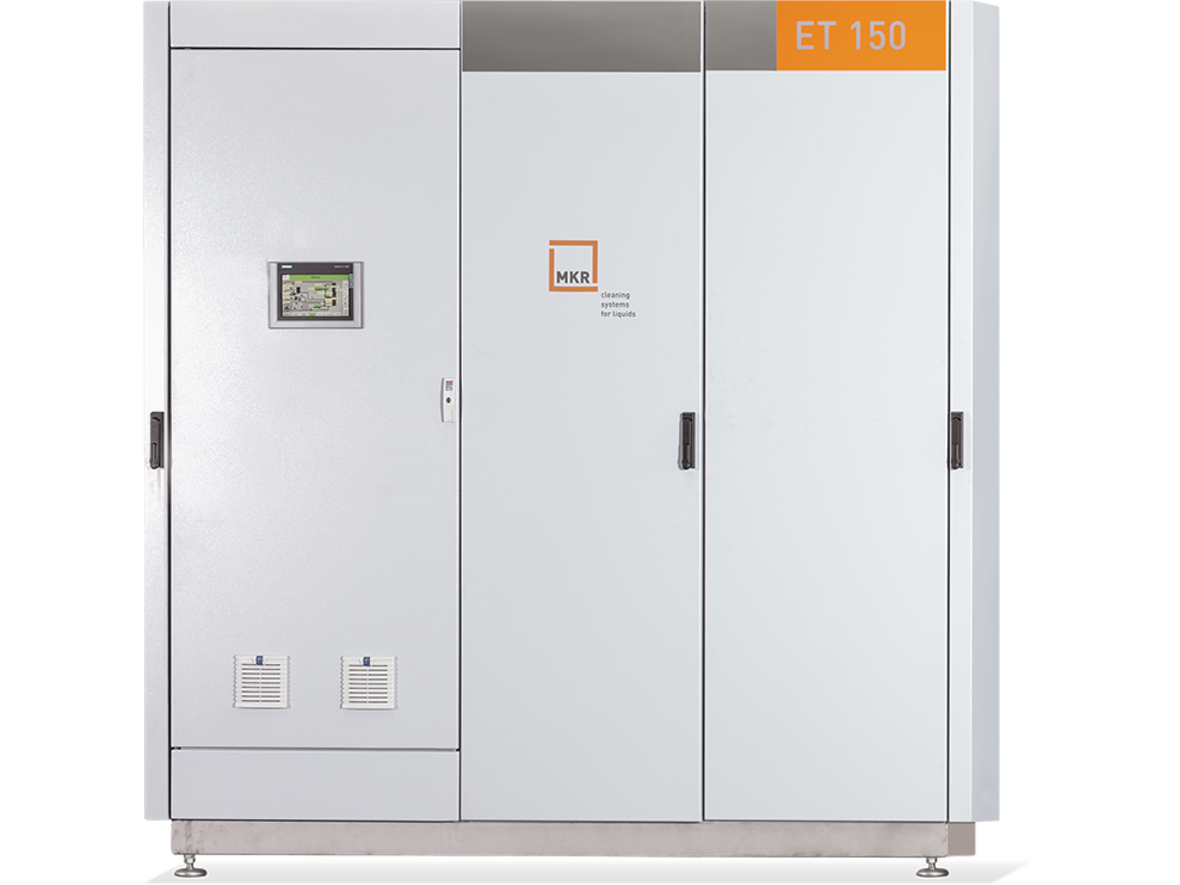
Evaporators
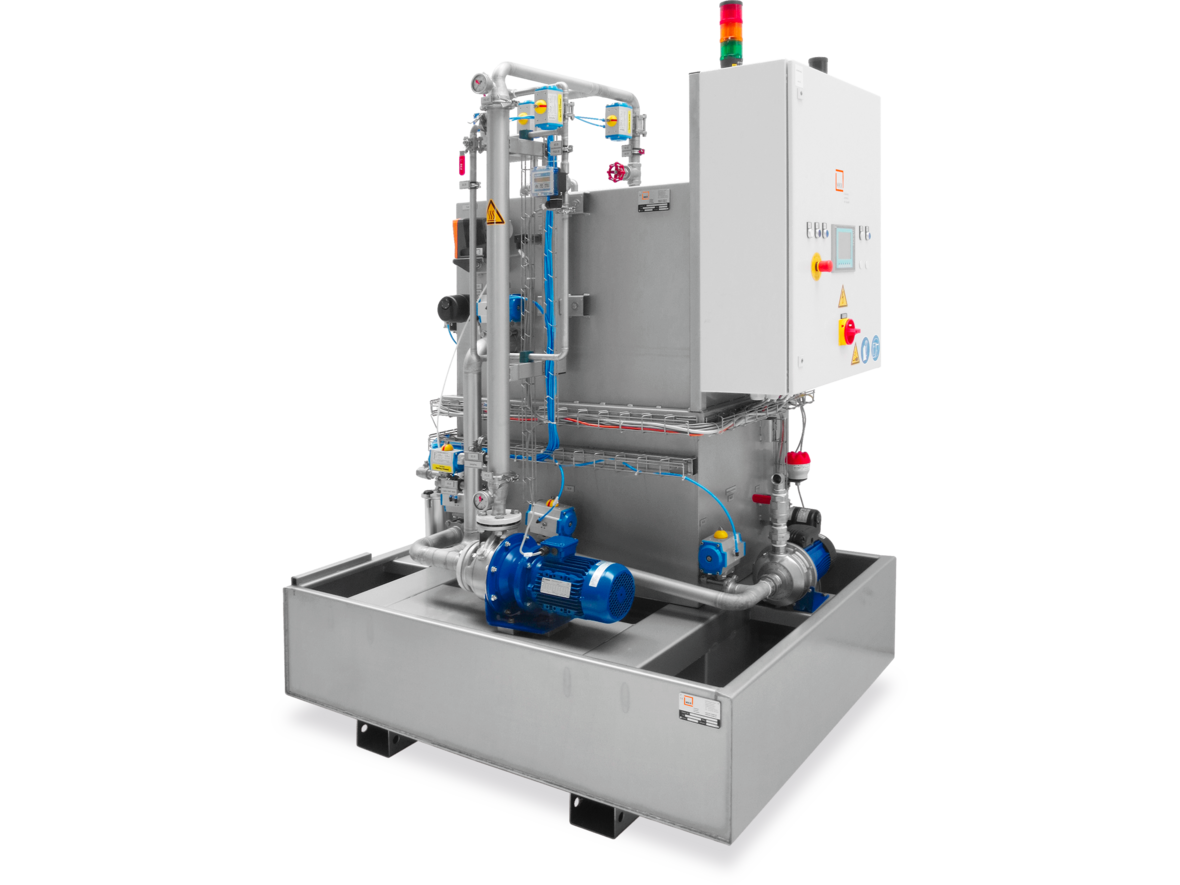
Filtration technology
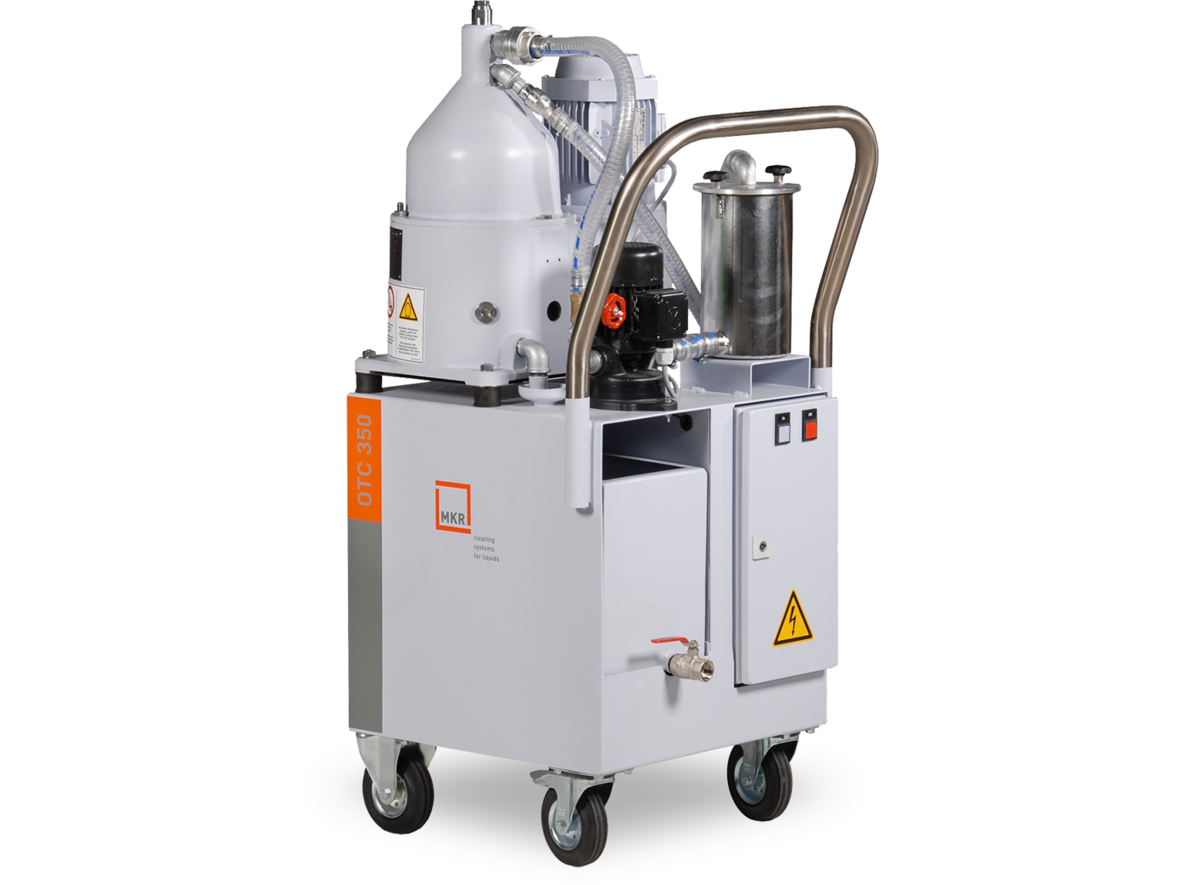
Disc stack centrifuges
The respective process medium is pumped from the machine tank and is then pumped through a centrifuge. The cleaned liquid, from which particles and tramp oils have been removed, is then returned to the production plant or washing system. This means that the media can be used longer – without quality loss, as confirmed by the leading manufacturers of process media. This means lower consumption and disposal costs. Another positive aspect is the ability to select the separator type for a specific interfering factor. Depending on the MKR machine type, separators with sludge removal, de-oiling or combined action are used. They enable cleaning capacities from 300 to 3000 litre per hour. In addition to tramp oils, ultrafine particles up to a size of 2 µm are removed. And what is also practical: The separators operate uniquely with the physical principles of
centrifugal force and gravity. They therefore require no filter aids whatsoever. THREE-PHASE DISC-STACK SEPARATOR It ensures complete and exact tramp oil and solid removal. In addition, water can be removed from hydraulic fluid cycles. MKR offers the choice between separators that collect solids and self-sludge removal separators. Tramp oil is absorbed and separated – regardless of whether the oil is floating on the surface or is dispersed in the metalworking fluid due to turbulence.
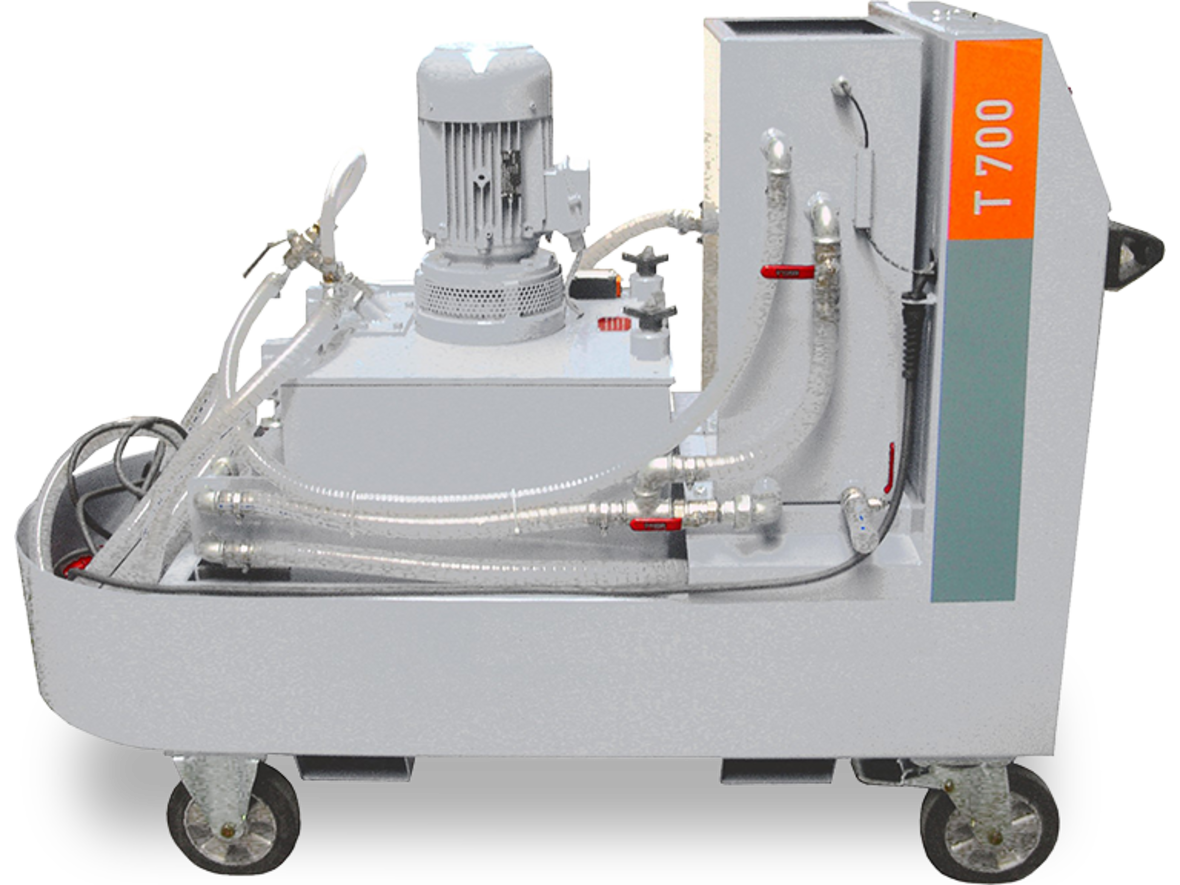
Drum centrifuges
The two/three-phase drum separator: This can be used to remove solids from emulsions with a high solids fraction in continuous operation. Centrifugal force ensures that the solids settle in the sludge insert. It
is possible to choose between separators that collect solids and self-sludge removal separators. In the third phase, tramp oil is removed.